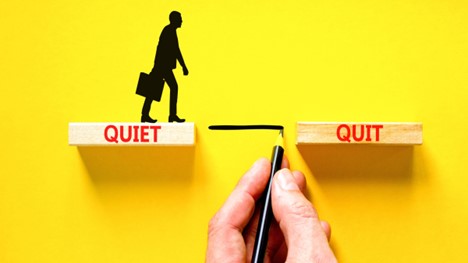
Using Nudges to Drive Performance: Insights from the Manufacturing Industry.
Using Nudges to Drive Performance: Insights from the Manufacturing Industry.
Nudges, which are subtle interventions designed to influence behavior without restricting choice, can be effective tools for driving performance in the manufacturing industry. By leveraging behavioral insights, manufacturers can implement nudges to improve safety, productivity, quality, and overall performance. Here are some insights on using nudges in the manufacturing industry:
Safety Nudges: Safety is a top priority in manufacturing. Nudges can be used to encourage safe behaviors and reduce workplace accidents. For example, placing visual cues or signs to remind employees to wear personal protective equipment (PPE), implementing safety checklists, or using color-coded markings to indicate potential hazards. These visual cues can serve as reminders and prompt safer behaviors.
Productivity Nudges: Nudges can be employed to enhance productivity in manufacturing processes. One example is providing feedback on individual or team performance. Displaying real-time production metrics or leaderboards can create a sense of competition and motivate employees to improve their performance. Additionally, implementing task-specific goals or targets can focus employee efforts and drive productivity.
Quality Nudges: Ensuring product quality is critical for manufacturing companies. Nudges can be used to promote quality control practices and reduce defects. For instance, implementing checklists or process reminders at various stages of production can help employees adhere to quality standards. Providing immediate feedback on quality metrics and recognizing individuals or teams for achieving high-quality outcomes can also reinforce desired behaviors.
Continuous Improvement Nudges: Nudges can facilitate a culture of continuous improvement in manufacturing. Implementing suggestion boxes or digital platforms where employees can submit improvement ideas encourages engagement and innovation. Recognizing and rewarding employees for their contributions to process improvements can reinforce the desired behavior and drive a culture of continuous learning and innovation.
Training and Skill Development Nudges: Nudges can be used to encourage employee engagement in training and skill development programs. For example, sending personalized reminders or notifications about training opportunities, breaking down training modules into smaller, manageable parts, or providing incentives for completing training courses can increase participation rates and enhance employee skill sets.
Environmental Sustainability Nudges: Nudges can also be applied to promote environmentally sustainable practices in manufacturing. Placing visual cues or reminders near waste disposal areas, encouraging energy-efficient behaviors, or implementing recycling programs with clear instructions can help employees make more sustainable choices.
Data-Driven Nudges: Leveraging data analytics and technology can enhance the effectiveness of nudges in manufacturing. Collecting and analyzing data on employee performance, safety incidents, quality metrics, and process inefficiencies can provide insights for targeted nudges. Automated systems or IoT-enabled devices can deliver timely nudges to employees based on real-time data, fostering behavior change and driving performance improvement.
It's important to note that when implementing nudges, manufacturers should consider the context, culture, and specific challenges within their organization. Regular evaluation and feedback loops are essential to assess the effectiveness of nudges and make necessary adjustments. By using nudges strategically, manufacturers can create a supportive environment that encourages positive behaviors and drives performance improvements throughout their operations.