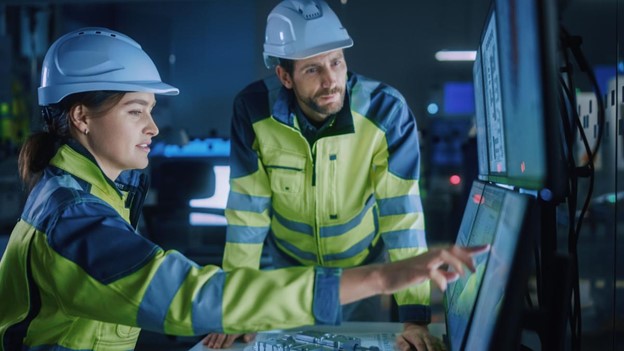
Nuances of Contextual Learning Recommendations for Employees in Manufacturing
Nuances of Contextual Learning Recommendations for Employees in Manufacturing
When it comes to recommending contextual learning for employees in the manufacturing industry, it's important to consider the specific nuances and challenges that are inherent to this sector. Here are some key factors to keep in mind:
Operational Environment: Manufacturing environments often involve specific machinery, equipment, and processes that are unique to each organization. Contextual learning should take into account the specific operational environment of the manufacturing facility and focus on providing employees with hands-on training and practical knowledge that directly applies to their roles and responsibilities.
Safety and Compliance: Safety is of utmost importance in the manufacturing industry. Any learning recommendations should prioritize safety training to ensure that employees are well-versed in safety protocols, procedures, and best practices. Compliance with relevant regulations and standards should also be emphasized.
Standard Operating Procedures (SOPs): Manufacturing operations often rely on standardized processes and procedures. Contextual learning should align with these SOPs and emphasize the importance of following established guidelines. Training programs can include interactive simulations, virtual reality (VR) modules, or practical demonstrations to provide employees with a clear understanding of the correct procedures.
Technical Skills Development: Manufacturing roles often require specific technical skills, such as machine operation, quality control, equipment maintenance, and process optimization. Contextual learning recommendations should prioritize skill development in these areas, utilizing a mix of theoretical knowledge and practical training sessions.
Lean Manufacturing and Continuous Improvement: The principles of lean manufacturing and continuous improvement are highly relevant in the manufacturing industry. Contextual learning should incorporate these concepts and provide employees with tools and techniques to identify and eliminate waste, streamline processes, and drive efficiency improvements.
Cross-functional Collaboration: Manufacturing operations involve collaboration among various teams and departments, including production, engineering, maintenance, and quality assurance. Contextual learning recommendations should promote cross-functional collaboration and provide opportunities for employees to understand and appreciate the roles and contributions of different teams.
Technological Advancements: The manufacturing industry is rapidly evolving with advancements in technology, such as automation, robotics, and data analytics. Contextual learning should keep employees updated on the latest technological trends and equip them with the necessary skills to adapt to technological changes and work effectively with advanced manufacturing systems.
Problem-Solving and Troubleshooting: Manufacturing processes often present unique challenges and require problem-solving skills. Contextual learning should focus on enhancing employees' ability to identify and troubleshoot issues, implement effective solutions, and make data-driven decisions to improve overall performance.
On-the-Job Training: Manufacturing employees benefit greatly from on-the-job training experiences. Contextual learning recommendations should include opportunities for employees to shadow experienced colleagues, participate in apprenticeship programs, or engage in job rotations to gain hands-on experience and practical insights.
Performance Monitoring and Feedback: Regular performance monitoring and feedback sessions are crucial in the manufacturing industry. Contextual learning recommendations should include mechanisms for managers and supervisors to provide constructive feedback, identify areas for improvement, and recognize exceptional performance.
Remember, contextual learning recommendations for manufacturing employees should be tailored to the specific organization's needs, taking into account the industry's unique characteristics and operational context. By providing targeted and relevant learning opportunities, you can empower employees to excel in their roles and contribute to the overall success of the manufacturing organization.