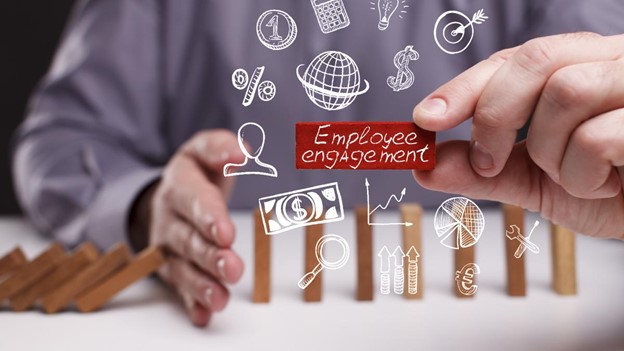
Nuances of Contextual Learning Recommendations for Employees in Indian Manufacturing
Nuances of Contextual Learning Recommendations for Employees in Indian Manufacturing
Contextual learning recommendations play a vital role in employee development and performance improvement, particularly in the Indian manufacturing sector. As an industry that requires specific skills and knowledge, providing employees with targeted and contextually relevant learning opportunities can enhance their capabilities and contribute to the overall success of manufacturing organizations. In this guide, we will explore the nuances of contextual learning recommendations for employees in the Indian manufacturing sector.
Assessing Skills and Knowledge Gaps: Before providing contextual learning recommendations, it is essential to assess the existing skills and knowledge gaps of employees. This can be done through performance evaluations, skills assessments, or surveys. By identifying the specific areas where employees lack proficiency or require further development, organizations can tailor their learning recommendations accordingly.
Understanding the Manufacturing Context: To provide effective contextual learning recommendations, it is crucial to understand the unique characteristics and challenges of the Indian manufacturing sector. This includes factors such as industry regulations, technological advancements, supply chain management, quality control, and safety protocols. A deep understanding of the manufacturing context helps identify the most relevant learning topics and methodologies.
Industry-Specific Training Programs: The Indian manufacturing sector encompasses a wide range of industries, including automotive, textiles, pharmaceuticals, electronics, and more. Each industry has its own set of skills and knowledge requirements. Providing industry-specific training programs tailored to the particular needs of employees can significantly enhance their performance. For example, in the automotive industry, employees may benefit from training in lean manufacturing, Six Sigma, or quality management systems.
Technology-driven Learning: The manufacturing sector in India is experiencing rapid technological advancements, including automation, robotics, Internet of Things (IoT), and data analytics. Incorporating technology-driven learning methods such as e-learning platforms, virtual reality simulations, or mobile apps can enhance employee engagement and effectiveness. These methods enable employees to acquire new skills and stay updated with emerging technologies in a flexible and interactive manner.
On-the-Job Training and Mentoring: Contextual learning recommendations should include on-the-job training opportunities and mentoring programs. Manufacturing employees often learn best through hands-on experience and guidance from experienced colleagues. Implementing job rotations, apprenticeships, or assigning mentors to new employees can facilitate knowledge transfer and skill development in a real-world manufacturing environment.
Soft Skills Development: In addition to technical competencies, soft skills are crucial for employees in the manufacturing sector. Effective communication, teamwork, problem-solving, leadership, and adaptability are essential skills that contribute to productivity and employee satisfaction. Incorporating soft skills training programs into contextual learning recommendations can foster well-rounded development and enhance overall performance.
Continuous Learning Culture: To ensure the long-term effectiveness of contextual learning recommendations, organizations need to foster a culture of continuous learning. Encouraging employees to embrace learning as an ongoing process and providing resources for self-directed learning can drive employee motivation and engagement. Creating platforms for knowledge sharing, such as internal forums or communities of practice, can also enhance the learning ecosystem within the organization.
In conclusion, contextual learning recommendations for employees in the Indian manufacturing sector should consider the specific skills and knowledge gaps, the unique characteristics of the manufacturing context, and industry-specific requirements. Incorporating technology-driven learning, on-the-job training, and mentoring programs, as well as emphasizing soft skills development and fostering a continuous learning culture, can contribute to the professional growth and performance improvement of manufacturing employees. By investing in contextually relevant learning initiatives, organizations can enhance their competitiveness, adapt to industry changes, and achieve sustainable success.