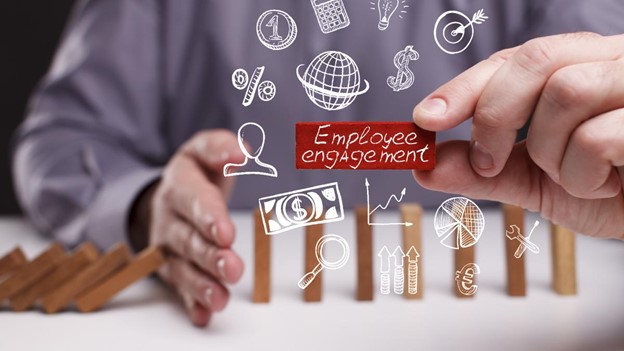
Need for skill gap analysis in Japan Manufactuing sectors
Need for skill gap analysis in Japan Manufactuing sectors
Japan is known for its advanced manufacturing industries, particularly in the automotive, electronics, and machinery sectors. Here are some key aspects of employee performance management in Japan's manufacturing sectors:
Kaizen: Kaizen is a Japanese philosophy that emphasizes continuous improvement in all aspects of an organization. In manufacturing, this philosophy is often used to optimize production processes and improve product quality. Employee performance management in Japanese manufacturing sectors often involves identifying opportunities for kaizen and encouraging employees to participate in these initiatives.
Training and Development: Japanese manufacturing companies place a strong emphasis on employee training and development. This includes both technical training to develop skills in areas such as manufacturing and engineering, as well as soft skills training to improve communication, problem-solving, and teamwork. Performance management in Japanese manufacturing often includes assessing employee training needs and providing opportunities for ongoing development.
Quality Control: Japanese manufacturing companies are known for their rigorous quality control standards. Employee performance management in these sectors often involves setting and monitoring quality metrics to ensure that products meet these standards. This may include training employees in quality control techniques, providing feedback on performance, and implementing continuous improvement initiatives.
Teamwork: Japanese manufacturing companies often emphasize teamwork and collaboration among employees. Performance management in these sectors may include assessing individual and team performance, providing feedback, and promoting a culture of collaboration and mutual support.
Overall, employee performance management in Japan's manufacturing sectors is characterized by a focus on continuous improvement, training and development, quality control, and teamwork. By emphasizing these key areas, companies can drive business success while also supporting employee growth and development.
Skill gap analysis is important in any industry, but particularly in Japan's manufacturing sectors, where technical skills and expertise are highly valued. Here are some reasons why skill gap analysis is necessary in Japanese manufacturing:
Aging Workforce: Many skilled workers in Japan's manufacturing industries are nearing retirement age, which means that there is a risk of losing valuable knowledge and expertise. Skill gap analysis can help identify areas where new workers may need additional training or support to fill these gaps and ensure that critical knowledge is not lost.
Technological Advancements: Japan's manufacturing industries are constantly evolving, with new technologies and processes being introduced regularly. Skill gap analysis can help identify areas where employees may need to develop new skills or expertise to keep up with these advancements and ensure that companies remain competitive.
Global Competition: Japanese manufacturing companies face stiff competition from other countries, particularly in Asia. Skill gap analysis can help identify areas where Japanese workers may be falling behind their global counterparts, and help companies develop strategies to stay competitive.
Changing Workforce Needs: As the nature of work changes, companies may need to adapt their workforce to new demands. Skill gap analysis can help identify areas where employees may need to develop new skills to stay relevant, such as in areas such as data analytics, automation, or digital transformation.
Overall, skill gap analysis is important in Japan's manufacturing sectors to ensure that employees have the skills and expertise they need to succeed in a rapidly changing industry. By identifying areas of weakness and investing in training and development, companies can support their workforce and drive business success.