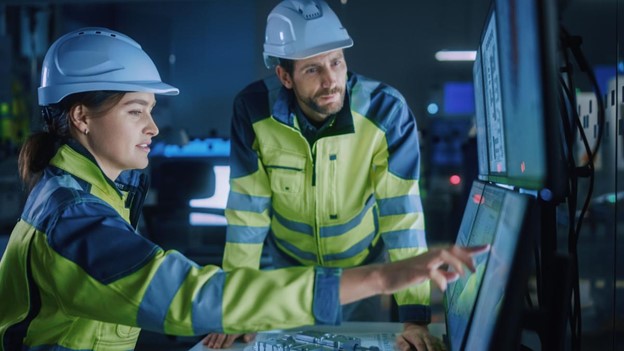
Future of Performance Management in Manufacturing: Predictions and Trends.
Future of Performance Management in Manufacturing: Predictions and Trends.
The future of performance management in the manufacturing industry is likely to be shaped by several trends and predictions. While the exact trajectory may vary, the following are some potential developments that could influence performance management in manufacturing:
Shift towards Continuous Feedback and Coaching: Traditional annual performance reviews are giving way to more frequent and ongoing feedback and coaching. Manufacturing companies are recognizing the need for real-time performance discussions to address issues promptly, support employee growth, and foster continuous improvement. Performance management systems will facilitate regular check-ins, feedback loops, and coaching conversations between managers and employees.
Emphasis on Skill Development and Upskilling: Manufacturing is becoming increasingly reliant on advanced technologies and automation. To keep pace with these changes, performance management will prioritize skill development and upskilling. Manufacturing companies will focus on identifying skill gaps, providing targeted training, and aligning performance goals with the development of new competencies required for evolving roles.
Adoption of Data Analytics and AI: Data analytics and artificial intelligence (AI) will play a significant role in performance management in manufacturing. Advanced analytics will enable the collection and analysis of performance data from various sources, such as production metrics, quality control, and employee feedback. AI algorithms can provide insights, predict performance trends, and offer recommendations for optimizing individual and team performance.
Goal Alignment and Cascading: Manufacturing organizations will increasingly emphasize goal alignment throughout the hierarchy. Performance management systems will enable the cascading of goals from the organizational level to individual employees, ensuring that each employee's objectives contribute to broader company objectives. This alignment enhances collaboration, accountability, and overall organizational performance.
Focus on Team and Collaborative Performance: Manufacturing operations often involve team-based work structures. In the future, performance management will place more emphasis on evaluating and rewarding team and collaborative performance. Performance metrics will be designed to assess team dynamics, cross-functional collaboration, and the ability to achieve shared objectives.
Integration with Digital Platforms and Tools: Digital platforms and tools will be integrated into performance management processes in manufacturing. These platforms may include performance tracking systems, employee engagement tools, collaboration platforms, and learning management systems. The integration of these tools will enable seamless data flow, facilitate communication, and provide a holistic view of performance.
Agility and Adaptability: The manufacturing industry is evolving rapidly, driven by technological advancements, market changes, and global dynamics. Performance management systems will need to be agile and adaptable to accommodate shifting priorities, changing goals, and dynamic performance metrics. Continuous feedback, goal adjustments, and agile performance planning will become key features of performance management in manufacturing.
Holistic Performance Assessment: Performance management in manufacturing will move beyond traditional metrics such as productivity and output. There will be an increased focus on holistic performance assessment, considering factors such as quality, safety, innovation, customer satisfaction, and employee engagement. This broader perspective will provide a comprehensive understanding of overall performance and enable organizations to drive sustainable success.
These predictions and trends provide a glimpse into the potential future of performance management in the manufacturing industry. However, it's important to note that the specific implementation and adoption of these trends may vary across organizations based on their unique needs, industry subsectors, and organizational cultures.