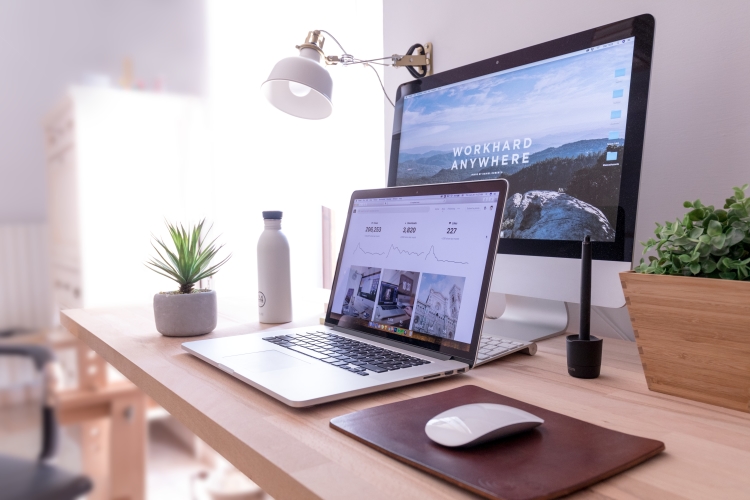
A guide to employee performance management in US Manufacturing Industries.
A guide to employee performance management in US Manufacturing Industries.
Manufacturing is a significant industry in the United States, employing millions of people and contributing significantly to the country's economy. Here are some of the largest manufacturing industries in the US:
Food and Beverage Manufacturing:
This is one of the largest manufacturing industries in the US and includes the production of a wide variety of food and drink products. This industry is responsible for employing a large number of people across the country.
Chemical Manufacturing:
Chemical manufacturing is another large industry in the US, with companies producing a range of chemical products, including plastics, synthetic rubber, and other chemicals used in various industries.
Transportation Equipment Manufacturing:
The US is a major producer of transportation equipment, including cars, trucks, airplanes, and ships. This industry is responsible for a significant number of jobs and contributes significantly to the country's economy.
Computer and Electronic Product Manufacturing:
The US is a significant producer of computer and electronic products, including computers, mobile devices, and communication equipment. This industry is responsible for a significant number of jobs and contributes significantly to the country's economy.
Employee performance management in US manufacturing industries is a process that involves setting clear performance expectations, providing regular feedback and coaching, evaluating performance, and recognizing and rewarding good performance. Here's a guide to employee performance management:
1.Set clear performance expectations:
Employees should be provided with clear job descriptions, performance standards, and goals that align with the organization's overall objectives. This includes setting specific, measurable, and achievable performance goals, identifying the key performance indicators, and outlining the expected outcomes. Performance goals should be aligned with the company's overall objectives. .
2.Provide regular feedback and coaching:
Regular feedback and coaching sessions should be conducted to help employees improve their performance. This includes providing constructive feedback, identifying areas for improvement, and offering guidance and support. This can include metrics related to production output, quality, safety, or other key performance indicators.
3.Evaluate performance:
Performance evaluations provide an opportunity to assess employee performance, identify areas for improvement, and recognize achievements. This can include conducting annual or quarterly performance reviews, using performance metrics, or setting up 360-degree feedback systems.
4.Recognize and reward good performance:
Good performance should be recognized and rewarded. This can include offering bonuses, promotions, or other incentives. .Recognition can include offering bonuses, promotions, or other incentives. Recognition can also include verbal praise, public recognition, or other forms of non-monetary recognition.
5.Provide opportunities for professional development:
Providing employees with opportunities for professional development can help them improve their skills and stay up-to-date with industry trends. This includes offering training and development programs, mentoring, or coaching.
6.Offer training and development opportunities:
Providing employees with opportunities for training and development can help them improve their skills and stay up-to-date with industry trends. This includes offering training and development programs, mentoring, or coaching.
7..Use technology to streamline the process:
Using technology can help streamline the performance management process, making it easier to track performance metrics, provide feedback, and evaluate performance. This includes using performance management software, data analytics tools, or other technologies that can help automate the process.
8.Use performance metrics:
Manufacturing industries rely heavily on performance metrics to measure employee performance. These can include metrics such as production output, quality control, waste reduction, and equipment downtime. By using these metrics, managers can assess employee performance and identify areas for improvement.
Manufacturing industries are constantly evolving, and employees need to keep up with new technology and processes. Providing opportunities for training and development can help employees improve their skills and stay up-to-date with industry trends.
Overall, effective employee performance management is critical for ensuring that employees are motivated, engaged, and productive. By providing clear performance expectations, regular feedback, and opportunities for recognition and professional development, organizations can improve employee satisfaction and ultimately achieve better outcomes for the organization and its customers.